News
Servicing Your Buchi Pressure Reactor
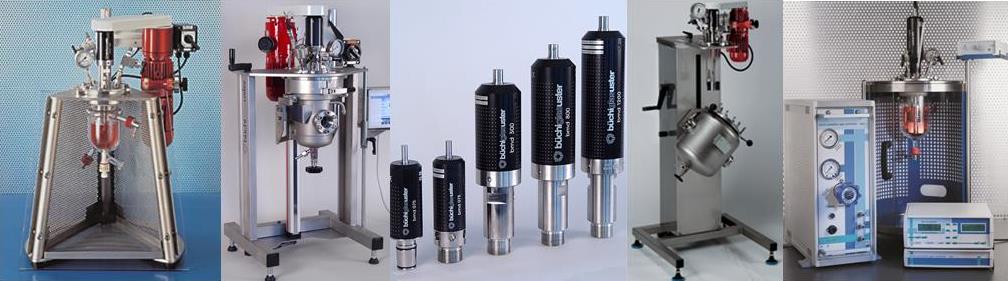
If you already own a Buchi pressure system – whether this is a 100ml Miniclave or a 20L BEP280/Kiloclave then you will know that it requires very little maintenance thanks to great Swiss design and robust construction. However, there are seals and bearings that do eventually wear and oil, belts, valves and rupture discs that need inspecting and occasionally are in need of replacement. Ken Kimble Ltd is here to support you whether it is to supply spare parts, advice or to provide an on-site service engineer. Indeed we are very proud of the fact that we have been supporting systems for over 40 years and have huge range of spares in stock for next day delivery.
If you are in the UK and a user of our pressure equipment your Health and Safety department will have probably identified the relevance of the Pressure Systems Safety Regulations (PSSR, 2000). The PSSR sets out the responsibilities of the pressure system Owner and mainly concerns larger systems where the product of pressure and volume is greater than 250bar.litres. However below this volume, which includes almost all the Buchi pressure systems we have supplied, there are indeed four sections which are very much applicable, including Section 12 which requires proper maintenance.
“All pressure equipment and systems should be properly maintained. There should be a maintenance programme for the system as a whole. It should take into account the system and equipment age, its uses and the environment”.
“The user of an installed system…….shall ensure that the system is properly maintained in good repair, so as to prevent danger.
Checks should be carried out to ensure that safety-related features are operating correctly. A fault affecting production is normally apparent within a short time whereas a fault in a safety critical part, such as a protective device, could remain undetected unless appropriate safety checks are included as part of the maintenance programme”.
The manuals that are supplied with the equipment show in detail the changing of various seals, rupture discs and for those systems with magnetic couplings, the bearing sets. We are happy to provide you with the latest versions of these manuals and to talk you through the steps necessary. For the larger systems such as the old BEP280 and the newer Ecoclave, Polyclave, Kiloclave, Versoclave and the high pressure models such as the Limbo and the Midiclave you might consider a visit from one of our factory-trained service engineers would be more appropriate and perhaps better satisfy the requirements of PSSR.
A service visit will include a very thorough dismantling, cleaning, change of seals and bearings, transmission oil change (where present), inspection and re-assembly. The system is then tested for leaks and functionality and a full report is made and discussed with the system owner. If there is a heater/chiller attached we have also been directly trained by both Huber and Julabo – you might like us to service these at the same time. If you have a Buchi BPC gas controller we can also arrange service and calibration.
Whether or not you decide that your system would benefit from a visit by one of our service engineers please feel free to call us for a relevant spares list and information on how to self-maintain your Buchi pressure system. Above all please let us help you to keep your system running safely.
For more information contact Ken Kimble Ltd, BuchiGlasUster agents for Ireland and the United Kingdom.
Date posted: 05-04-2017
Expanded Glass Reactor Range
Wide Range of Glass Reactors for Kilo Lab and Scale-Up 5 litres to 250 litres
Glass reaction and distillation systems built around vessels from 5 to 250 litres. We have been supplying the ChemReactor range of reactor and distillation systems for many years, with vessel sizes from 15 litres to 60 litres designed to fit in a walk in fume cupboard. Larger systems up to 250 litres with integrated glass superstructure also use the Büchiflex flexible glass joint for ease of use, good vacuum tight joints and easy reconfiguration should the process change.
The new MidiPilot range (20-30 litres) bridges the gap between these larger scale-up systems, often used for GMP manufacture of APIs and the smaller laboratory scale MiniPilot systems from 5 to 15 litres.
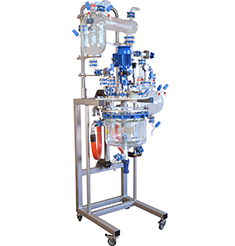
These reactors are already being successfully used around the world for chemical synthesis, low temperature chemistry, crystallisation, refluxing, multi-phase extractions, azeotropic and vacuum distillation.
At the heart of each system is a top quality jacketed glass vessel rated for full vacuum and up to +1bar (over-pressure protection is fitted as standard) and
-60°C….200°C (minus 90°C with the triple-walled vessel option). Unlike most lab-based glass reactors, the lid is made from PFA-coated stainless steel as found on the Production-scale versions. This makes the system extremely robust and therefore able to withstand the rigours of the busy Process Development or scale-up facility.
The system is totally modular – the strong lid and fully welded stainless steel frame are able to support substantial distillation, reflux and feed vessel (10L) components. Solids-charging is facilitated by a large and easily accessible loading port. A Cleaning-in Place (CIP) spray nozzle can also be easily accommodated. The glass parts utilise the very same self-draining Büchiflex connection system used on our large glass plant. A lift option enables the vessel to be lowered easily for cleaning, loading and even exchange with alternative reactors. The frame can be supplied for bench-top mounting or with integral wheeled trolley making it very easy to store outside the walk-in fume cupboard when not in use. To assist further chemical processing, the MidiPilot can be easily connected to one of a range of ancillary modules including mixing vessels, scrubbers, dryers and vacuum filtration units.
As with the large-scale kit, a dry-running ATEX rated mechanical seal is employed as well as a very powerful ATEX motor. The stirrer shaft has interchangeable stirrer shapes such as impeller, turbine and anchor which can be PFA or glass lined steel. A common issue with this scale is inadequate mixing and again we address this by using our proven ChemReactor baffle design with its integral Pt100.
Whether it is the CE marking, ATEX rating, FDA approval, the use of Production-standard components or the fact that you will be supported by the leading professional glass-plant manufacturer, we believe, that for the first time, the demands of the important scale-up phase are fully addressed by the MidiPilot.
Why settle for scaled-up lab glass when you can invest in the quality of a scaled-down production plant?
Date posted: 14-02-2017
Hydrogenation Systems
HYDROGENATION: Functional, safe and reliable equipment from Buchi
Hydrogenation chemistry demands that your equipment is both reliable and safe and therefore we have designed a complete package with safe Hydrogenation in mind from the outset. In particular Hydrogenation reactions often involve the combination of flammable solvent, pyrophoric catalyst, explosive hydrogen and of course not forgetting the hazards of your reactants and products. Furthermore this is typically pressurised. It is situations like this that you need to have complete trust in your equipment. Made in Switzerland to the highest standards and all relevant European safety regulations, BuchiGlasUster have been designing and manufacturing pressure systems for over 30 years and examples are to be found all around the world from Universities to some of the largest companies in the Oil, Pharma and Electronics sectors.
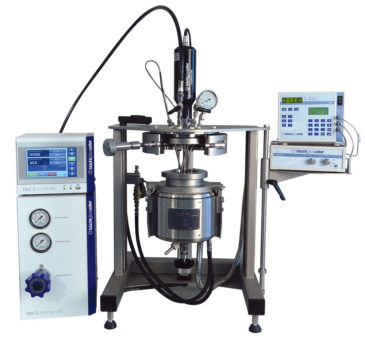
Not only are the reactor systems we produce safe they are also designed to be easy to use with features such as fast-action-closure and easily exchangeable vessels (the Kiloclave for example can accept 500ml or 20L vessels and all those in between). We supply both sparge tubes and hollow stirrer shafts which when combined with our turbine agitator ensures both efficient mixing and hydrogen gas entrainment. There is also a sampling system which can be operated during the reaction thus avoiding possible stalling of the catalyst. Baskets are available should you want to contain your catalyst and there are various options for safely filtering the product whilst still under pressure.
Hydrogen gas can be dosed in with the Buchi BPC2 – a sophisticated instrument which can maintain a set-pressure of hydrogen and measure the gas in moles (or litres) to do so. Unlike mass flow controllers the BPC can dose over both a very wide range of pressure and delivery rates. Unlike mass flow meters the BPC2 has a number of built-in safety features which prevent uncontrolled flow of hydrogen gas. The technology has been well developed over many years and they have been supplied to many companies performing hydrogenations from catalyst manufacturers to R&D and Pilot Plants belonging to the largest Pharmaceutical companies in the world.
In terms of monitoring we supply the BLS2 software package which can display your real-time hydrogen uptake and hence reaction profile. This not only tells you when your reaction is complete but how this varies over time. Thus on the graph you can see just when hydrogen uptake began, evidence of rate limiting factors, evidence of 2-stage hydrogenations and where is the most efficient point to stop the reaction. By varying temperature, pressure, catalyst type and loading (etc) you can easily monitor the effect on reaction rate in order to optimise your hydrogenation. The software can issue a Hydrogenation Report for your records.
Ken Kimble (Reactor Vessels) Limited are BuchiGlasUster agents for the United Kingdom and Ireland.
For more information please contact us.
Date posted: 14-02-2017
Economic Small-Scale Pressure Reactors
Our range of small-scale 10 – 300ml pressure reactors in both glass and steel are already widely used in cutting edge research and development both in industry and academia. Current applications include catalyst screening, hydrogenation, crystallisation, hydrothermal and nanoparticle synthesis as well as material testing and corrosion testing.
Click here to explore our range in more depth. 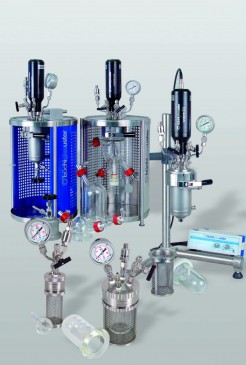
Recent additions to the range, following customer requests, include PTFE liners and metal vessels available rated up to 300oC. We think that these small scale pressure vessels are a good entry level introduction for those investigating pressure reactions before scaling up to one of our larger, more versatile systems. We are pleased to be able to offer special lower pricing on a number of these smaller vessels. Please contact us for details.
The Miniclave, Tinyclave and Picoclave are the smallest systems within our huge range of pressure reactors. The range extends to several 100 litres in volume. We use the same design principles for the entire range which makes for a smooth transition, if scale-up should be required.
If you are intending to work on a scale of up to 300ml, operate between -1…100 bar and less than 300°C then we are confident that we can supply a very economical system to suit your application. We have fully inert versions for very corrosive chemistry and several units with integral magnetically coupled stirring and jacketed vessels for efficient mixing and optimum temperature control. These features are particularly useful for Process Development.
The following table highlights some of the basic features of these small scale systems:

If you need to work outside these parameters please let us know, as there are many possibilities to go beyond these limits and indeed there are 12 other systems in the range enabling you to work at much larger volumes, pressures and/or temperatures. Metal reactors are commonly made from stainless steel but we also supply them in tantalum, titanium, Hastelloy, Inconel etc.
In terms of quality and safety, these Swiss-manufactured reactors are the best you can buy and with the substantial reductions currently on offer we are confident that you will agree they are great value for money.
Please contact us so that we can discuss your application.
Date posted: 14-01-2016
Systag FlexyPAT: Automation Technology for Chemical Process Lab
Ken Kimble Ltd has a long history of supplying and supporting not only simple stirred-vessel systems, but also those incorporating automation (for hydrogenation, parallel synthesis and azeotropic distillation etc). We are now excited to introduce FlexyPAT – a combination of hardware and software which enables you to automatically perform and monitor your chemistry. The FlexyPAT is designed and manufactured in Switzerland by Systag – a respected partner in the pharmaceutical industry for over 50 years and a market leader in automation solutions for all aspects of chemical process development.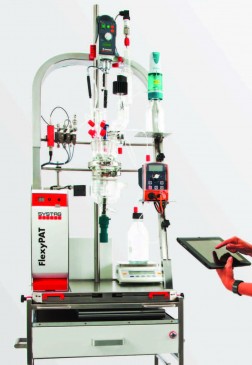
A key feature of the FlexyPAT is that you are able to utilise your existing reactor vessels, heater/chillers, pumps and balances; this not only reduces the cost but familiarity of the equipment accelerates system acceptance. Of course we can also supply a ‘Turn-Key’ solution that includes all the relevant equipment for your process.
At the heart of the FlexyPAT is a module to which all the relevant reactor system parts are connected, very much in a ‘plug and play’ manner. This includes the heater/chiller, stirrer motor, balance(s), syringe pump(s), dosing pump(s) and online sensors (such as turbidity, midIR, FTIR, particle size, pH and temperature). There is even the ability to automatically take photographs of the vessel contents at either set times or when, for example, the turbidity has reached a certain value. FlexyPAT uses cable recognition technology allowing sensor devices to be instantly recognised when connected.
A PC is loaded with FlexySys application software and this in turn is used to control and monitor the FlexyPAT and therefore your reactor system.
The system is very flexible in terms of being able to integrate both existing equipment and additional devices either at the start or later on as your future chemical processing dictates. Not only can ancillary equipment such as dosing pumps be added but up to five additional complete reactors can be controlled from a single FlexyPAT module.
The FlexySYS software will allow the operator to control the reactor remotely either on-demand or to set up and run complex ‘recipes’ with multiple steps.
These recipes are very easy to prepare using the ‘drag-and-drop’ method with a built-in logic check. More than a simple series of steps, a recipe can include loops and jumps to be set up in response to certain recorded values. This feedback from the sensors enables not only something as simple as pH control but also the temperature could be controlled in response to turbidity, for example. A very useful feature is a Hold step which can be used to take a sample for analysis.
The user-friendly control screen presents an animated depiction of the hardware in use and the operator is simply able to click on each device and control it. In terms of Process Development an important feature is that the settings, operations and analytical measurements are stored automatically and compiled as a batch record.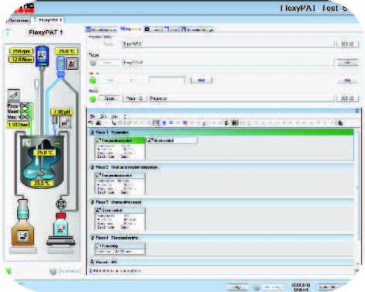
With the appropriate hardware in place, the FlexyPAT is able to control the following:
- Temperature (internal and jacket)
- Stirrer speed
- Addition – either gravimetric or volumetric
- pH (through addition)
- Reflux distillation
- Pressure/vacuum
- Hydrogenation
…and the following data can be monitored/calculated and stored:
- Temperature
- pH
- Stirrer speed and torque
- Boiling point determination
- Isothermal heat flow calorimetry
- Turbidity
- FTIR data
- Particle size measurements (including ability to interface with Lasentec)
In addition to the above, the FlexySYS software includes a set of easy-to-use programmes which enable you to perform calibration of the PT100 and pH probes as well as the PID settings for the temperature control circuit. A record of these actions can be appended to your batch record.
Should you decide to source the reactor itself from us we offer the especially designed FlexyPAT Caddy which has a jacketed glass (or metal) vessel (various volumes available)held within a stainless steel frame and base. It is designed to sit on a bench within the fume cupboard but if you have a walk-in FC or you would like to be able to easily remove it and store elsewhere we will also supply the FlexyPAT Trolley onto which the Caddy can be positioned and locked in place. The frame of the Caddy is cleverly designed to support the FlexyPAT as well as various hardware devices such as pumps, probes and the stirrer motor whilst hiding the cables and giving the operator maximum access to the vessel and lid. Alternatively, if you already have support framework at the back of the fume cupboard we can utilise this instead.
Typical areas of application for the FlexyPAT are the following:
- Process Development
- Process Engineering
- Process Analytical Technology
- Scale-up and Scale-down
- Small-scale Production
- Morphology
- Research and Development
Whether you are looking for a complete Turn-Key automated reactor system or a means to control your existing equipment please call us to discuss your process and we will customise a system for your needs.
Date posted: 14-01-2016
MidiPilot: small scale Pilot Plant for the fume cupboard…
Ken Kimble is excited to reveal the Buchi midiPilot which utilises the very same robust components from Buchi’s large scale equipment but on the 20 to 30L scale.
Buchi are already highly respected for their extensive range of quality Production-scale glass plant including their 250L ChemReactors, Nutsche filters, mixing vessels and scrubbers. We believe their latest innovation is perfect for the cGMP facility where perhaps API’s are being made or indeed any environment where a reliable, robust reactor is required. These reactors are already being successfully used around the world for chemical synthesis, low temperature chemistry, crystallisation, refluxing, multi-phase extractions, azeotropic and vacuum distillation.
At the heart of each system is a top quality jacketed glass vessel rated for full vacuum and up to +1bar (over-pressure protection is fitted as standard) and -60°C….200°C (minus 90°C with the triple-walled vessel option). Unlike most lab-based glass reactors, the lid is made from PFA-coated stainless steel as found on the Production-scale versions. This makes the system extremely robust and therefore able to withstand the rigours of the busy Process Development or scale-up facility.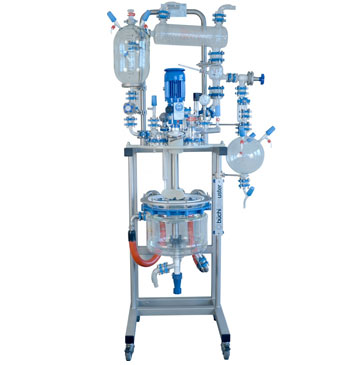
The system is totally modular – the strong lid and fully welded stainless steel frame are able to support substantial distillation, reflux and feed vessel (10L) components. Solids-charging is facilitated by a large and easily accessible loading port. A Cleaning-in Place (CIP) spray nozzle can also be easily accommodated. The glass parts utilise the very same self-draining Buchi-Flex connection system used on our large glass plant. A lift option enables the vessel to be lowered easily for cleaning, loading and even exchange with alternative reactors. The frame can be supplied for bench-top mounting or with integral wheeled trolley making it very easy to store outside the walk-in fume cupboard when not in use. To assist further chemical processing, the midiPilot can be easily connected to one of a range of ancillary Buchi modules including mixing vessels, scrubbers, dryers and vacuum filtration units.
As with the large-scale kit, a dry-running mechanical seal is employed as well as a very powerful ATEX motor. The stirrer shaft has interchangeable stirrer shapes such as impeller, turbine and anchor which can be PFA or glass lined steel. A common issue with this scale is inadequate mixing and again we address this by using our proven Chemreactor baffle design with its integral PT100.
Whether it is the CE marking, ATEX rating, FDA approved, the use of Production-standard components or the fact that you will be supported by the leading professional glass-plant manufacturer, we believe, that for the first time, the demands of the important scale-up phase are fully addressed by the midiPilot.
Why settle for scaled-up lab glass when you can invest in the quality of a scaled-down production plant?
Date posted: 15-10-2015
BPC2 – accurate hydrogen charging system
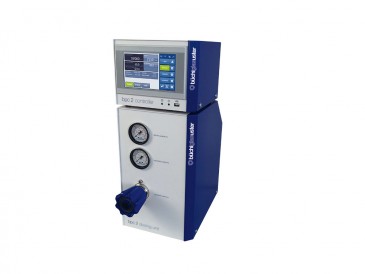
BPC2 Gas Control Unit for Hydrogenation
The Pressflow Controller from Buchi (known as the BPC) was originally designed over 30 years ago and since then it has become the de facto industry-standard equipment for performing hydrogenation reactions. They are currently installed in virtually every major pharmaceutical company as well as many catalyst manufacturers, agrochemical companies and research institutions throughout UK and Ireland – the fact that 95% of these instruments are still working safely and accurately after all these years is a testament to quality Swiss engineering and strong after-sales support from Ken Kimble Ltd.
For those who have not used the BPC, it is a volumetric hydrogen dosing instrument which is able to measure the gas it charges into a reaction vessel in order to maintain the required process pressure. Unlike the mass flow controller, it can perform this task extremely accurately and over a very wide range of pressures and flow rates without the need for re-calibration. Other gases can be used such as oxygen, carbon dioxide, carbon monoxide, ethylene, propylene etc. The progress of the reaction can be observed without the need for regular sampling (which can lead to stalling of the hydrogenation process) by observing the molar uptake of hydrogen. This data can also be used to perform Design of Experiment (DoE) studies in order to optimise your process.
After several years of development which has included consultation with existing users of the BPC and the availability of new and more accurate technology we are proud to announce the launch of its successor, the BPC2.
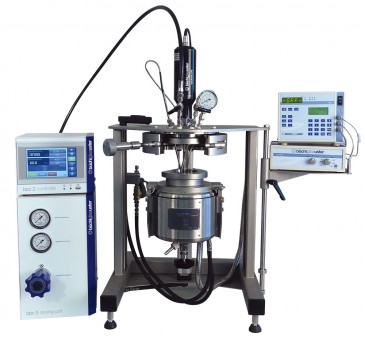
BPC2 Gas Control Unit with Midiclave for Hydrogenation
For existing users this new version has a number of significant improvements such as a continuous flow function. This gives the operator the option to allow a set flow of hydrogen into and out of the vessel headspace which is useful where the process evolves a gas as well as consuming the hydrogen. The sensors within the unit are now up to 10x more accurate. A very useful feature is the touch screen which is used to both control and graphically monitor the hydrogen consumption over time – something only possible in the past with additional PC and software. The graph can for example plot the reaction temperature, hydrogen consumption (in moles or litre) and reaction pressure. The screen can be observed remotely via Ethernet connection. In addition the data can now be transferred easily directly to a memory ‘stick’ and therefore manipulated remotely. Perhaps the most useful addition is the ability to set up automatic purge cycles (for both inert and active gases) which can be combined with an automatic leak test of the reaction vessel. This not only makes preparation easier but in terms of safety this also ensures that the required number of purges are carried out and that the system is leak tight before proceeding. Finally a range of gases other than hydrogen can be used – the pre-loaded data can be unlocked on request.
Hydrogenation chemistry demands that your equipment is both safe and reliable as it often involves the combination of flammable solvent, pyrophoric catalyst, explosive hydrogen and of course any hazards of your reactants and products. Furthermore this is typically pressurised. It is situations like this we understand that you need to have complete trust in your equipment. Made in Switzerland to the highest standards and all relevant European safety regulations, Buchi have been designing and manufacturing pressure systems including the BPC for over 30 years and examples are to be found all around the world. The BPC2 has a number of safety features built in such as leak detection and abnormal flow/consumption set points as well as the automatic purge cycles, leak tests and alarm set points mentioned above.
The BPC2 is just one instrument in a range of pressure equipment that we have been supplying since 1976. This includes a very wide range of jacketed vessels from 10ml to 100’s of litres and hollow stirrer shafts which when combined with our turbine agitator ensures both efficient mixing and excellent gas entrainment. There is also a sampling system which can be operated during the reaction, catalyst baskets, filtration capsules and pressure burettes. Temperature control is either electrical or by the use of oil pumped from appropriately selected thermostats which we also supply. We make this equipment from a wide variety of materials including stainless steel, Hastelloy, Titanium, Tantalum, PTFE and glass-lined steel.
For more information, including an on-site demonstration, please contact us.
Ken Kimble Ltd, BuchiGlasUster agents for Ireland and the United Kingdom.
Date posted: 23-04-2015
INERT PRESSURE REACTORS: Non-metallic system overview
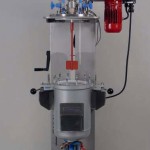
Kiloclave Inert
BuchiGlasUster is renowned for manufacturing the highest quality pressure systems for the chemical industry. Usually these consist of a glass or metal vessel with a metal coverplate and various metal accessories such as the stirrer shaft and PT100 probe. Although we offer a wide range of metals such as stainless steel, Hastelloy, Titanium, Zirconium or Tantalum, sometimes the chemistry, often with highly corrosive media, demands that no metal is present. For these chemically aggressive reactions we can offer systems that have wetted parts made from inert materials only such as PTFE, PFA, glass, ceramic and PEEK.
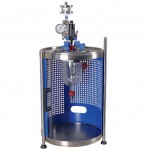
Inertclave
We offer a range of five such inert systems covering a reaction scale from 100ml to 20L and are rated for pressures up to 6 bar and temperature up to 180°C. The vessels are either glass or glass-lined steel and the coverplates are either PTFE or PEEK. For the systems with integral stirring, Buchi have developed excellent leak-proof ceramic magnetic drives. Seals are either PTFE or Kalrez. Please note that these temperatures, pressure and volumes are standard but can often be exceeded upon request.
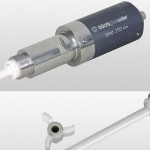
Ceramic Magnetic Coupling
All systems are designed, manufactured and tested in Switzerland according to the Pressure Equipment Directive and AD2000 and are CE marked. ATEX versions are also available. In addition to the vessel and coverplate, each system is supplied complete with a stand (for either the bench top or walk-in fume cupboard), pressure gauge, rupture disc, PT100, inlet/outlet valves stirrer drive assemblies, tools and spares.
Please contact us in order to discuss your requirements or to request the latest pressure equipment catalogue.
Ken Kimble (Reactor Vessels) Limited are BuchiGlasUster agents for the United Kingdom and Ireland.
Date posted: 11-03-2015
KILOCLAVE: From grams to kilos using one system
Like all Buchi pressure systems a range of vessels can be simply attached to the one frame and coverplate. The Kiloclave can accept a range of eight standard interchangeable vessels from 500 ml to 20 litres which makes the system very adaptable and cost effective. For example, Process Design work could be performed on the 100 ml scale in the 500 ml vessel and after a quick vessel change you have a system which can be used as a Pilot Plant for the manufacture of kilo quantities – API for clinical trials for example. The Kiloclave is suitable for a wide range of chemical reactions including hydrogenation where the use of the gas entrainment agitator and BPC2 hydrogen gas dosing system make your process highly efficient and controllable as well as providing the chemist with invaluable reaction data.
The Swiss design and build quality ensure that this exchange of vessels is quick and easy; there is even an integral lift which can not only lower the vessel but can enable the vessel to be rotated for inspection /cleaning. In terms of material of construction we manufacture using stainless steel 316, Hastelloy, Tantalum, Titanium, Inconel, Zirconium and now we have a new all-inert version with glass-lined steel vessels. A magnetic coupling and ATEX drive/transmission unit delivers high torque and is completely leak free.
As standard, vessels are rated for pressures up to 60bar depending on vessel size; however we regularly customise systems to exactly match our customers’ needs and this may include vessels rated up to 350 bar. Vessels can be supplied with and without sight glasses and there is also an option of fast-action-closure which enables the release of the vessel from the coverplate in just a few seconds.
As with all Buchi pressure systems they are fully compliant with all the relevant European safety standards. They are also ‘ready to go’ as each system includes vessel, frame, pressure gauge, baffle, PT100, rupture disc assembly, flush-mounted bottom outlet valve, agitator parts, spares and tools. The vessels can be supplied jacketed (and therefore needing a heater/chiller) or with integral electric heating. The standard temperature range is -10°C to +250°C. There is also an option to have the system mobile which can be very useful where walk-in fume cupboard space is limited.
The Kiloclave is safe, versatile, reliable, user friendly and extremely well engineered. It is not surprising therefore that it, and its’ predecessor the BEP280, is to be found in all the major Pharmaceutical companies around the world whether in the R&D laboratory or indeed the Pilot Plant.
Ken Kimble (Reactor Vessels) Limited are BuchiGlasUster agents for the United Kingdom and Ireland.
For more information please contact us.
Date posted: 05-02-2015
HYDROGENATION: Functional, safe and reliable equipment from Buchi
Hydrogenation chemistry demands that your equipment is both safe and reliable as it often involves the combination of flammable solvent, pyrophoric catalyst, explosive hydrogen and of course not forgetting the hazards of your reactants and products. Furthermore this is typically pressurised. It is situations li
ke this that you need to have complete trust in your equipment. Made in Switzerland to the highest standards and all relevant European safety regulations, BuchiGlasUster have been designing and manufacturing pressure systems for over 30 years and examples are to be found all around the world from Universities to some of the largest companies in the Oil, Pharma and Electronics sectors.
Not only are the reactor systems we produce safe they are also designed to be easy to use with features such as fast-action-closure and easily exchangeable vessels (the Kiloclave for example can accept 500ml or 20L vessels and all those in between. We supply both sparge tubes and hollow stirrer shafts which when combined with our turbine agitator ensures both efficient mixing and hydrogen gas entrainment. There is also a sampling system which can be operated during the reaction thus avoiding possible stalling of the catalyst. Baskets are also available should you want to contain your catalyst and there are various options for safely filtering the product whilst still under pressure.
Hydrogen gas can be dosed in with the Buchi BPC2 – a sophisticated instrument which can maintain a set-pressure of hydrogen and measure the gas in moles (or litres) to do so. Unlike mass flow controllers the BPC can dose over both a very wide range of pressure and delivery rates. The technology has been well developed over many years and they have been supplied to many companies performing hydrogenations from catalyst manufacturers to R&D and Pilot Plants belonging to the largest Pharmaceutical companies in the world.
In terms of monitoring we supply the BLS2 software package which can display your real-time hydrogen uptake and hence reaction profile. This not only tells you when your reaction is complete but how this varies over time. Thus on the graph you can see just when hydrogen uptake began, evidence of rate limiting factors, evidence of 2-stage hydrogenations and where is the most efficient point to stop the reaction. By varying temperature, pressure, catalyst type and loading etc. you can easily compare conditions in order to optimise your hydrogenation. The software can issue a Hydrogenation Report for your records.
Ken Kimble (Reactor Vessels) Limited are BuchiGlasUster agents for the United Kingdom and Ireland.
For more information please contact us.
Date posted: 04-02-2015
PILOTCLAVES: Custom Built Pressure Reactor Systems
Buchi manufacture 14 standard reactor systems each with many variables such as vessel size, pressure and temperature rating and material of construction. Add to this the choice of many extra features such as sampling, fast action closure and lifting mechanisms it gives rise to literally 100’s of variants.
However we also design and manufacture bespoke systems. These may include for example, a number of vessels mounted on a skid. For scale-up into Pilot plant or indeed Production, larger vessels than 20L are often required. We also design and construct more complex systems which may include additional pressurised processes such as addition, reflux, distillation and down-stream filtration. Often these will need to be suitable for ATEX zoned areas and there may also be a level of automation from simple remote stirrer speed display to full monitoring and control.
We call these unique systems Pilotclaves such as these recent examples:
- 100L, 50bar hydrogenation reactor, skid mounted
- 20L system in scaffold frame with reflux capability
- 100L, 40bar reactor with pressure distillation overhead
- 3x20L vessels mounted in a single frame, fully automated
- 100L, 60bar vessel, wall mounted
- 20L, 350°C, 350 bar Hastelloy with electric lift
For over 3 decades Ken Kimble Ltd have been the Buchi Agents for UK and Ireland and we very much pride ourselves in the support we have given to industry and academia whether in the installation and service of equipment, on-going technical support and supply of spare parts – often for systems supplied in the last century.We are very proud of these systems which are designed and made in Switzerland by our highly skilled engineering department. Buchi has been leading the field for over 65 years and the company complies with the most stringent International safety standards (EC machinery Directive, ATEX, TA Luft, PED). When you have to work under pressure with often hazardous conditions you can 100% rely on quality Swiss engineering.
Whatever your pressurised process or scale, please contact us and we will either match your requirement with one of our off-the-shelf systems or start the process of designing and constructing your very own Pilotclave!
Date posted: 01-12-2014
Ken Kimble – New website
We have recently launched our new website. We hope you like it and find it even easier to navigate. Should you have any questions please do not hesitate to contact us.
Date posted: 01-12-2014